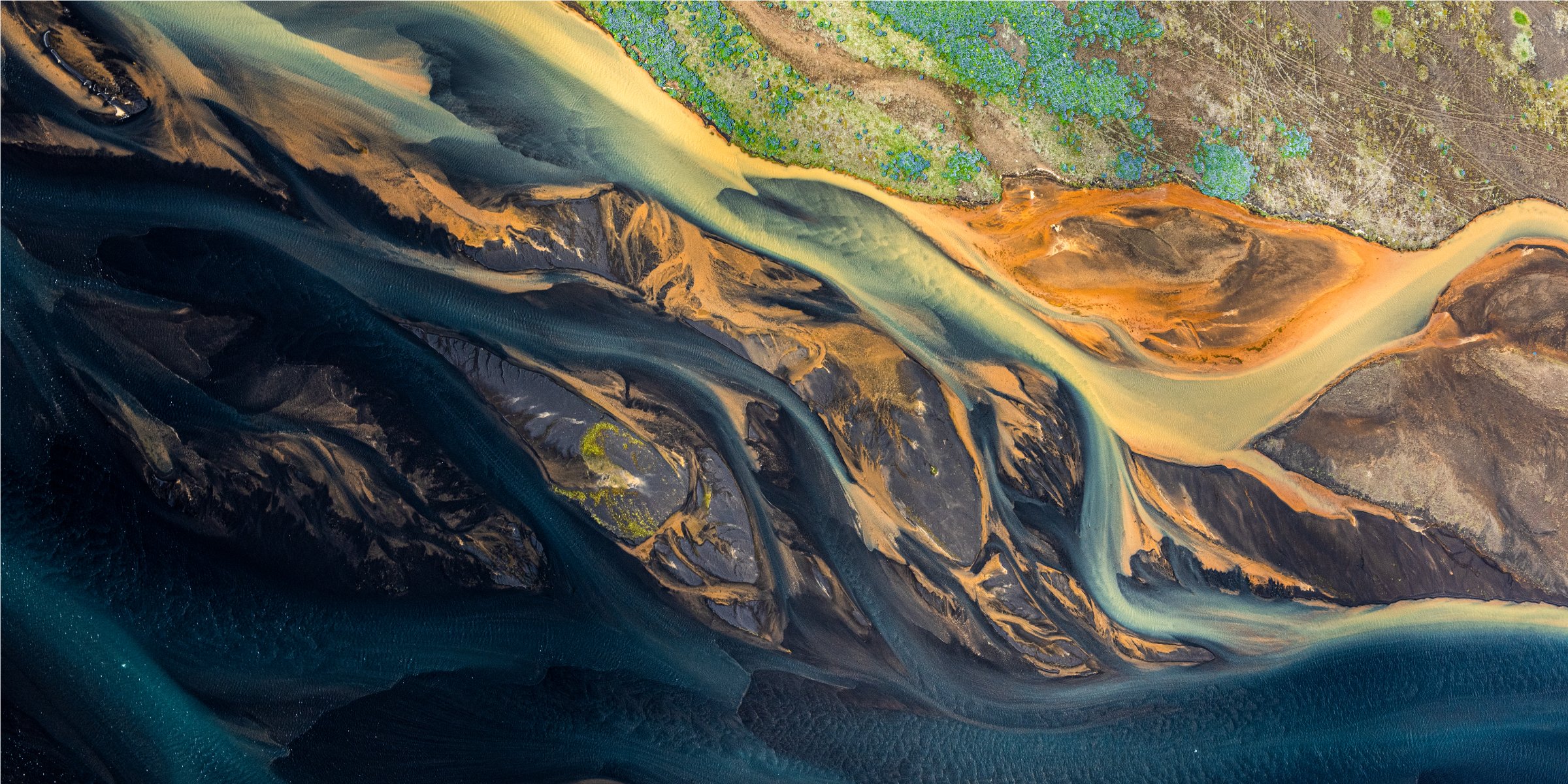
San Marcos Company Aims to Energize U.S. Magnets Supply
October 15, 2022
San Antonio Express News: San Marcos Company Aims to Energize U.S. Magnets Supply
By Eric Killelea
SAN MARCOS — In Noveon Magnetics Inc.’s lobby in San Marcos, CEO Scott Dunn stood before a table as he handled small glass bulbs filled with powdered forms of rare earth minerals that are key to the future of clean energy technologies.
Dunn examined the rare earth powders, which had been mined and chemically separated from concentrated ore and precipitated as oxides. The company puts those powders through a complex process in which they are converted into metal that gets alloyed and broken into near-nano crystals, which are heated through patented technology, pressed and magnetized.
Dunn picked up a 6-pound, demagnetized block off the table.
“This is a neodymium magnet,” he said. “It doesn’t need a current to become a magnet. That is what we produce.”
Since 2014, privately owned Noveon has been working to recycle rare earth minerals and end-of-life magnets from electronic waste to make the coveted neodymium magnets. The minerals improve the performance of those magnets, which facilitate the conversion of electricity into motion.
The U.S. government and private sector is hungry for the magnets, which are essential to making air conditioners, washing machines and cooling fan motors in computers and microwaves. They’re also used in MRI machines, wind turbines, robots, fighter jets and missiles.
With support from the federal government, Noveon — the only known company in the U.S. producing “sintered” neodymium magnets — envisions itself reducing this country’s dependence on China for rare earth minerals. The company, formerly known as Urban Mining Co., plans to expand its unique recycling business model to produce magnets, thereby avoiding higher mining prices and preventing shortages in the coming years.
Rare Earths
For decades, China has “dominated” mining and processing rare earth materials, said Kelly Nash, a professor who studies them at the University of Texas at San Antonio.
“The rare earths aren’t rare; they’re found in large deposits,” Nash said. “But the U.S. has a lot of restrictions around mining practices.”
She said extracting rare earth minerals without creating pollution is very difficult and that the U.S lacks the type of large-scale production seen in China, mostly because of regulations to control pollution.
“It’s a very dirty process to mine rare earths,” she said, “and it takes a lot of energy.”
After China drove up rare earth mineral prices by choking supply in 2010, companies started to build such businesses in the United States. But China quickly reversed its position, causing prices to drop and undercutting efforts to build an American mining industry.
The Trump administration in 2018 created an ambitious plan to ramp up domestic capacity and move supply chain operations to the U.S. Similarly, the Biden administration in March invoked the Defense Production Act to boost domestic production of raw materials to reduce U.S. dependence on foreign supply chains. The Defense Department has invested millions of dollars in the country’s one operational rare earth mine in Mountain Pass, Calif. MP Materials, the privately owned rare earth materials company headquartered in Nevada, has been working to modernize the facility, but the company sends the ores it mines to China for processing.
The Defense Department also designated money to Lynas Corp., an Australian company extracting ores from a mine in its county, which entered its bid in partnership with Blue Line Corp., a processing company based in San Antonio.
Still, a lack of domestic mining operations remains.
Neodymium Magnets
The Biden administration is also considering ways to mine neodymium and increase domestic production of neodymium magnets, which Nash called “the strongest magnets on Earth.”
A technician works in Noveon Magnetics Inc.’s processing facility in San Marcos. The company recycles rare earth minerals from used electronics to produce magnets used in many high-tech products.
Magnets “make electrical process more efficient,” Nash said, which results in the high demand for them.
“The magnetic field is interdisciplinary related to the electric field,” she said. “You can take magnetic energy and dump it into the electric powered devices in a vehicle.”
Last month, Biden avoided trade fights by not imposing tariffs on neodymium magnets that come mainly from China, though also from Japan and Europe. A report from the U.S. Department of Commerce shows that China produced 75 percent of American sintered neodymium magnets and recommended steps to increase domestic production.
Meanwhile, the Defense Department has awarded $35 million in funding to Noveon, the lone domestic company to use the sintering process to make the magnets for clients across industry sectors, including electric vehicles, energy, artificial intelligence and robotics, medical and more. The company is also seeking funding opportunities from the U.S. Department of Energy.
Ramping Up Production
Amid high demand, Noveon said it expects top-line revenue to hit $250 million over the next three years as the company seeks to capture a slice of the global market estimated to reach $79 billion by 2030.
Noveon, which has spent months installing equipment and testing the recycling process, seeks to boost production to manufacture 2,000 metric tons of magnets annually. Within Five to seven years, the company projects increasing that rate to 10,000 tons per year. Global production of magnets is roughly 170,000 tons.
Noveon also plans to build more facilities.
Noveon’s 150,000-square-foot headquarters sits on 10 acres. The company wants to grow on 100 acres that it has bought in San Marcos. The company has been searching across Texas and the U.S., as well as internationally, for sites to build other locations.
“Noveon has a strategic interest in Europe and will be exploring future international expansion opportunities,” the company said.
The expansion means hiring, and the company plans to increase its workforce to more than 100 employees by 2023. It had 25 employees in 2020.
Origin Story
In 2012, the U.S. was looking for ways to wean itself off Chinese rare earth minerals when Noveon’s founding members met at a conference in Nagasaki, Japan.
They included:
Dunn, from Maryland, Dunn who had attended the U.S. Naval Academy before finishing his bachelor’s degree at the University of Southern California.
Peter Afiuny, another USC graduate.
Miha Zakotnik, the chief technology officer and a scientist from Slovenia who earned a doctorate in material science from the University of Birmingham in England.
Catalina Oana Tudor, from Romania, who earned a doctorate in computer science from the University of Delaware.
They had spent time in Japan and China learning about metals and minerals industries.
Noveon Magnetics Inc. recycles rare earth minerals from used electronics at its processing facility in San Marcos to produce magnets used in many high-tech products.
After meeting, they began splitting their time between China and Delaware to figure out how to recycle rare earths, and they “stumbled” onto a new patented technology that could make magnets “in an altogether better and novel way,” Dunn said.
“The bigger stroke was there would be an ability to totally decentralize the supply chain and do something immediately without waiting 15 years for the (U.S. Environmental Protection Agency) to approve a mine and for it to come online, to at least mitigate, if not in some cases remove, some of the dependence on traditional Chinese supply chain materials,” Dunn said.
In 2016, the company received $25 million in series A funding and stood up a 10,000-square-foot research lab and facility near Austin-Bergstrom International Airport. Two years later, the company started building the magnet facility in San Marcos, which proved to have a less expensive real-estate market than Austin. By 2020, the company started recycling rare earth minerals and making magnets.
At that time, the Defense Department entered into a $28.8 million agreement with the company — before its name change — “to assist in developing a domestic source” for neodymium magnets.
The magnets “are essential components for many DOD programs that enable miniaturization and high performance of guidance, propulsion and power systems,” the Defense Department said. “This investment will enable Urban Mining Company to maintain and protect critical workforce capabilities during the disruption caused by COVID-19 while strengthening a vital domestic supply chain of rare earth materials.”
Since then, Noveon said it has made deals with partners, including Blue Line Corp., to recycle rare earth minerals and old magnets from “electric motors from e-mobility applications, automation devices, robotics, as well as wind turbines, electric vehicles, hard disk drives from data centers, and more.”
Noveon said it also can “source virgin/pure materials from domestic and international, allied partners to produce high-quality magnets.”
24-Hour Facility
At Noveon’s San Marcos facility, Dunn took a flight of stairs to the second floor, above the rare earth minerals and computer science labs, and strode past employees sitting in the open office, pausing to praise one staffer for her motorcycle helmet on her desk.
The loquacious Dunn entered the nearby kitchen overlooking the operational space with 60-foot-tall ceilings and large, heavy orange machines used for the alloy, powder and vacuumed sintering processes.
“You’re looking at a gigantic, concrete box on steroids,” Dunn said. “It’s almost like a giant oven that is about as high tech as it [expletive] gets.”
Dunn was relieved to get the equipment delivered and installed amid the COVID-19 pandemic.
“We got slammed, absolutely hammered by COVID,” Dunn said. “We have tons of international equipment, and equipment wasn’t showing up.”
Noveon has been mostly running 10-hour shifts, in a sort of test mode, and has not reached full capacity.
But looking forward, Dunn said the company is in a ramping-up phase this month and plans to start consistent, around-the-clock operations early next year.
“We basically have very specific customer-demand requirements, which are three times the size of this facility fully built out,” he said. “The tricky part is, let’s not get too far ahead of ourselves in terms of risk. Let’s engineer out any remaining risk items we think are possibly unknown on the horizon, and we’re going to get even more aggressive on expansion.”
By Eric Killelea