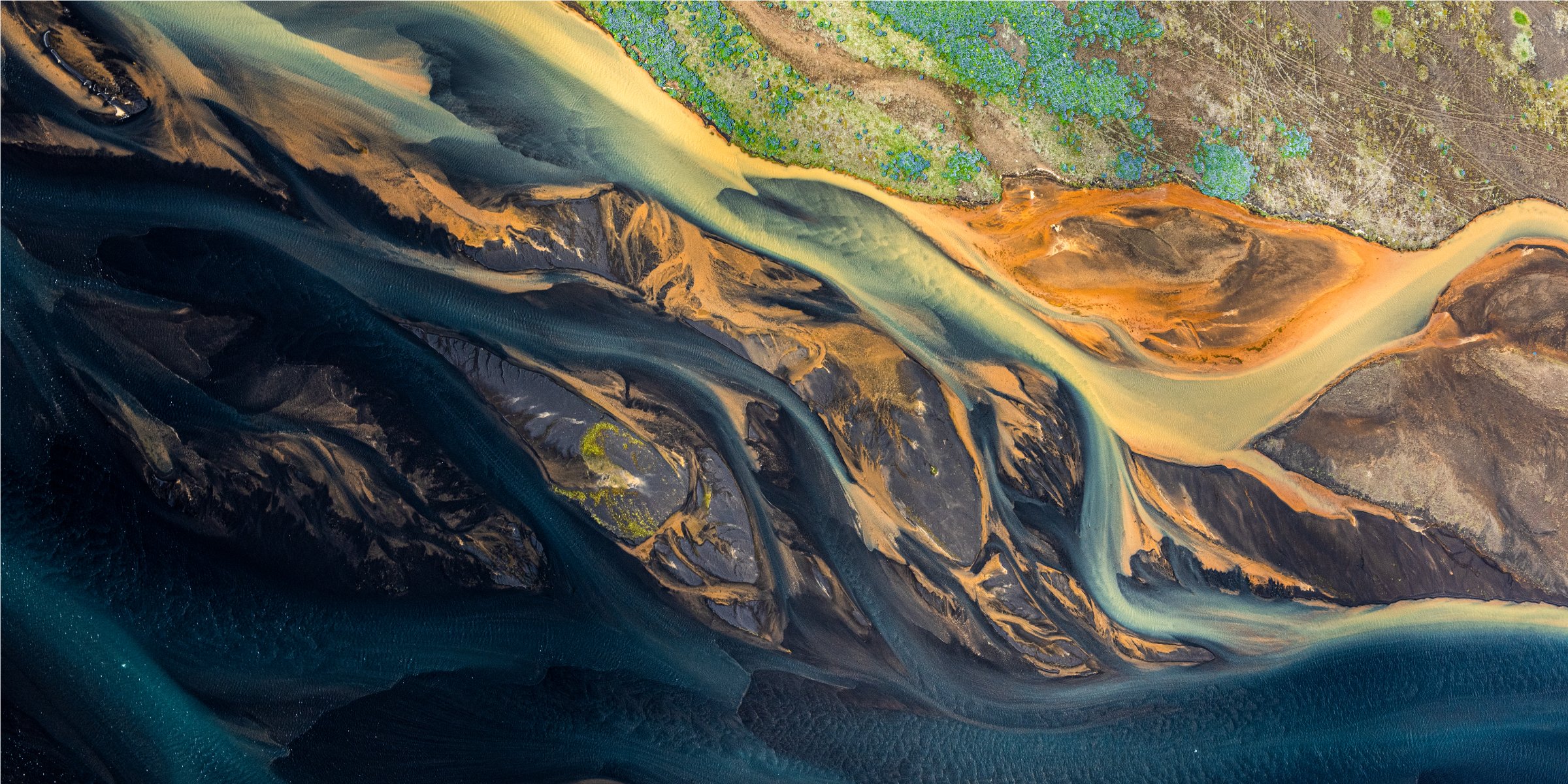
How Recycled EV Traction Drive Motors Can Help Unlock an Electric Future
March, 2023
How Recycled EV Traction Drive Motors Can Help Unlock an Electric Future
Year over year, we’ve seen a rapid rise in demand for electric vehicles (EVs) and hybrid electric vehicles (HEVs). Last year, EV sales in the United States increased by 65%, surpassing more than 800,000 annual EV sales for the first time in history. Moreover, in 2021 U.S. HEV sales jumped 76% to 801,550 vehicles, accounting for 5% of U.S. light vehicle sales that year.
As Americans continue to seek out new ways to lower their carbon footprint and EVs and HEVs become more cost competitive and sustainable in the long-term, demand will only continue to rise.
Transportation is currently the largest source of greenhouse gas (GHG) emissions in the United States and accounts for 29% of total GHG emissions nationwide. In an effort to combat overall GHG emissions and position the U.S as a leader in the fight against pollution, President Biden has set the ambitious goal of achieving a 50-52% reduction from 2005 levels in economy-wide net greenhouse gas pollution by 2030.
In order to reach this goal, the Biden Administration has enacted major legislation such as the Inflation Reduction Act (IRA) and the Infrastructure Investment and Jobs Act (IIJA); both of which aim to tackle transportation emissions by incentivizing the manufacturing and adoption of EVs. As a result of these incentives, almost every major automotive original equipment manufacturer (OEM) has publicly announced plans to increase the production of battery-powered EVs by 2030.
How The Inflation Reduction Act (IRA) Aims To Grow The Domestic Supply Chain for Clean Vehicles
Rare Earth Magnets: The Key to Meeting Rising Demand
As demand for EVs and HEVs continues to grow, so will demand for the NdFeB rare earth magnets needed to power electric motors, thereby introducing a new challenge to America’s vision for a low-carbon, electrified future. In order to meet rising demand for these magnets, we must begin to build out a domestic rare earth supply chain strong enough to power all the clean energy technologies, including EVs and HEVs, that we need in order to fight climate change.
Rare earth permanent magnets are a crucial component of virtually all electric technology, including the electric traction drive motors that power battery-powered EVs and HEVs. Notably, each individual electric traction drive motor requires 1-2kg of NdFeB magnets to function, and it is estimated that between 90-100% of battery EVs and HEVs will rely on synchronous traction motors using NdFeB magnets by 2025.
Despite concerns regarding the vast amounts of materials needed to manufacture electric vehicles, evidence suggests that emissions reductions associated with EV and HEV adoption outweigh environmental disturbances and waste associated with mining and manufacturing.
According to a Life Cycle Analysis (LCA) study conducted by the University of Michigan, the direct emissions generated from driving an internal combustion engine vehicle over its lifetime are far higher than the total lifecycle emissions of an EV, including those associated with both manufacturing and charging. Specifically, the study found that, on average, lifetime emissions from battery-powered EV sedans were 35% of the emissions created from an internal-combustion sedan, and electric SUVs produced 37% of the emissions of a gasoline-powered counterpart throughout their respective lifecycles.
However, given the inevitable expansion of rare earth mining and NdFeB magnet manufacturing that will come along with a clean vehicle revolution, it will be incredibly important to build a sustainable, independent rare earth supply chain that minimizes the use of virgin materials and subsequent waste as we work to meet rising demand.
Building a Sustainable and Independent Rare Earth Infrastructure
The existing supply chain for NdFeB rare earth magnets is highly centralized and unstable, and the U.S relies almost entirely on China for materials sourcing and manufacturing. Currently, China controls 58% of global rare earth mining output, 89% of oxide separation, 90% of rare earth metallization, and 92% of the global NdFeB magnet and magnet alloy market.
While the U.S must focus on building a secure domestic supply chain for NdFeB rare earth magnets, developing the infrastructure to mine and manufacture the materials we need will likely take years, and there are additional environmental costs associated with the harmful process of mining rare earth minerals. Therefore, in order to meet rising demand for clean energy technologies such as EVs, as well as our ambitious sustainability goals, we must identify circular solutions that focus on recycling rare earth magnetic material from end-of-life traction drive motors to create new NdFeB magnets that are just as powerful as those they replace.
Roughly 12 million vehicles are estimated to be scrapped in North America every year, and over 12% are vehicles with hybrid EV traction drive systems that have the potential to be recycled. This amounts to more than 1,500 tons of NdFeB rare earth magnet material that is currently being discarded when it could and should be supporting a sustainable domestic rare earth supply chain.
A circular economy for end-of-life electric and hybrid electric traction drive motors will allow us to bypass supply chain and national security concerns while also creating a more sustainable path toward electrification that bypasses the environmental consequences of mining. Right now, perfectly usable NdFeB rare earth magnets are being incinerated by large-scale vehicle recyclers as part of a larger metal recovery process. This means that critical NdFeB rare earth magnets are being treated as contaminants rather than being recycled. Yet, if we were to recycle rare earth magnetic materials from discarded traction drive motors rather than treat them as waste, it is estimated that by 2030 there will be enough end-of-life NdFeB magnet feedstock to power 250 million electric vehicles without significant environmental harm.
Prioritizing Recycling Solutions for End-of-Life Rare Earth Materials
Noveon is currently the only domestic producer of sintered NdFeB permanent magnets, the specific type of rare earth magnet used to power traction drive electric motors. Noveon is also the first company in history to develop recycling solutions for end-of-life magnet material, proving that the path to electrification can and should be a sustainable one.
As policymakers work to boost domestic rare earth magnet production to meet the demands of an electric future, reduce emissions, and accelerate a low-carbon economy, they must also prioritize building a reverse supply chain where discarded rare earth materials from earlier generations of the automotive and energy sectors can be manufactured into a new generation of applications.
Recycling EV and hybrid EV traction drive motors will allow the U.S to build a more robust domestic rare earth magnet supply chain, meet the rising demand for rare earth permanent magnets, and help usher in an electric future. With the growing threats to our supply chain, now is the time for Washingon to prioritize and invest in recycling solutions for end-of-life electric and hybrid vehicle traction drive motors.