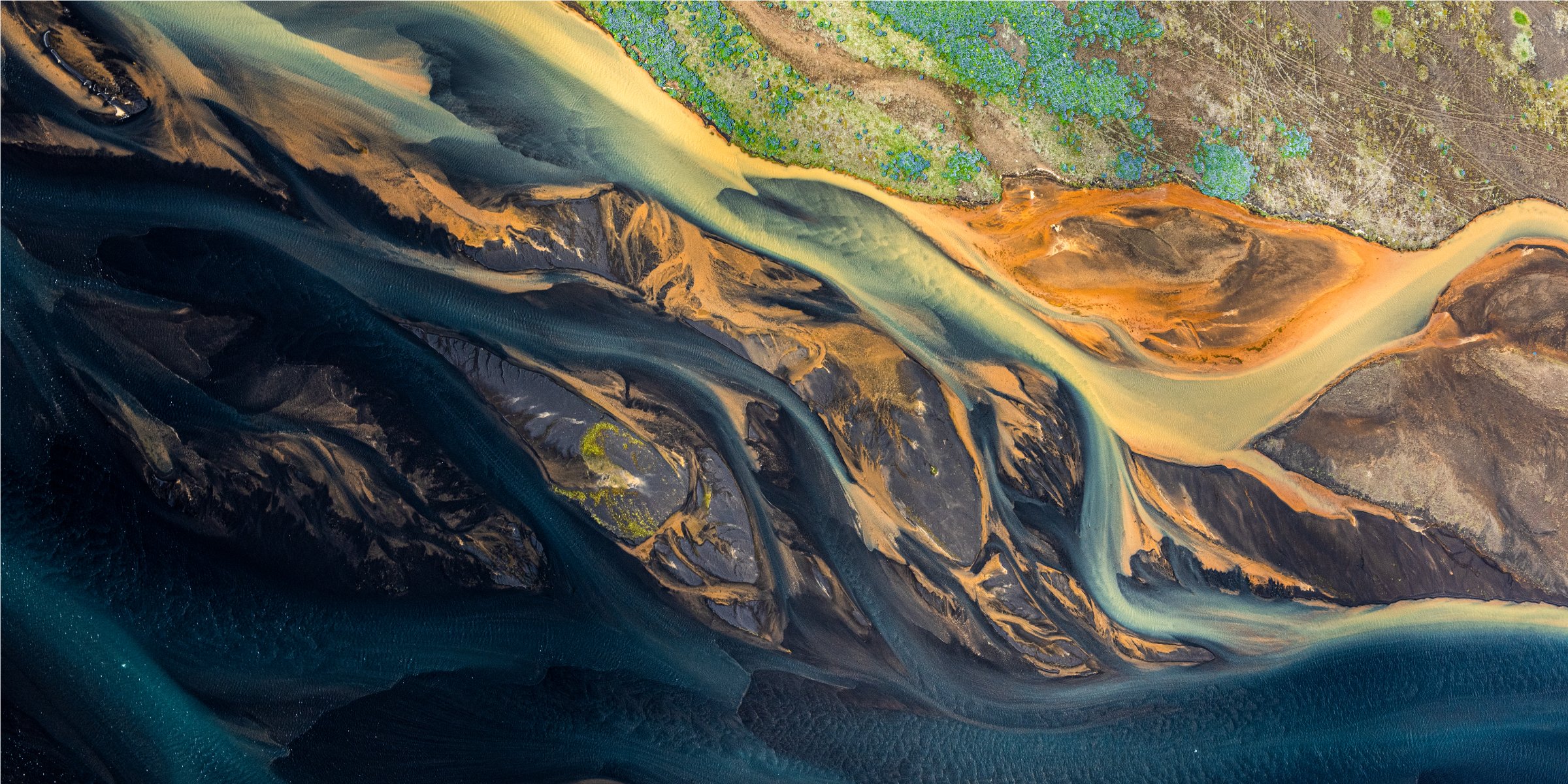
Rare Earth NdFeB Magnets Explained
January, 2023
Rare Earth NdFeB Magnets Explained
The earliest signs of permanent magnet use was for the compass around ~2500 BC. New magnetic material innovations did not occur until the early twentieth century. Over the course of the last one hundred years new material discoveries are pushing the boundaries of permanent magnet performance, and supporting the development of new technology critical to a carbon-neutral advanced society.
As we enter into a new industrial revolution in the age of electrification, rare earth neodymium-iron-boron (NdFeB) magnets play a critical role in building a high-tech, renewable energy future. They are currently the most widely-used type of rare earth magnet on the market and the most powerful commercially available permanent magnet.
Rare earth NdFeB magnets power some of the most innovative applications that are critical to the development of our ever-growing sustainable, electric infrastructure. Some of the many applications of NdFeB magnets include electric propulsion systems for land, sea, and air mobility, robotics, flight actuation and guidance, power generation, pumps, diagnostic imaging, sensors, data recording, and more.
Additional Examples of NdFeB Magnet Applications By Sector
Renewable Power Generation
Hybrid and Direct-Drive Wind Turbines, Solar Farms, Hydroelectric Power Stations
HEV and EV traction-drive motors, Starter motors, Anti-lock braking systems (ABS), Motor drives for wipers, Injection pumps, Fans, Power windows, power door locks, Power seats, Loudspeakers, Eddy current brakes, Alternators
Automotive
Magnetic anchoring and guidance systems, Retractors, Robotic cauterizers, High-speed motors for drills, Dentures Orthodontics, Orthopaedics, Ferromagnetic probes, Cancer cell separators, Magnetomotive artificial hearts, NMR / MRI body scanners
Medical
DC motors for showers, Washing machines, Drills, Low voltage DC drives for cordless appliances, Loudspeakers for TV and Audio, TV beam correction and focusing device, Compact-disc drives, Home computers, Video Recorders, Clocks
Consumer Electronics & Appliances
Loudspeakers, Microphones, Telephone ringers, Vibrating motors, Electro-acoustic pick-ups, Switches and relays
Telecommunications
Data Processing
Disc drives and actuators, Stepping motors, Printers
Sensors, Contactless switches, NMR spectrometer, Energy meter disc, Electro-mechanical transducers, Crossed field tubes, Flux-transfer trip device, Dampers.
Electronic and Instrumentation
Robotics, Magnetic separators, Magnetic bearings, Servo-motor drives, Lifting apparatus, Brakes and clutches, Switches, Relays
Industrial Motion Control & Automation
Cooling pumps, Centrifugal pumps, Positive displacement pumps, Fans, Blowers and other industrial motors, pumps and compressors used in Heating, Ventilation, Air Conditioning and Refrigeration (HVACR)
Industrial Motors, Pump, & Compressors
Frictionless bearings, Stepping motors, Couplings, Instrumentation, Traveling wave tubes, Auto-compass, Flight actuation motors
Aerospace & Defense
Oil and Gas
Pumps, Cooling systems, Pipeline Inspection Gantries, High precision drills
There are two types of rare earth NdFeB magnets, bonded and sintered, and they are classified based on the manufacturing process used to create them.
Bonded NdFeB Magnets
Bonded NdFeB magnets are created through injection molding, a manufacturing process that involves extruding melt-spun ribbon-like powdered material combined with polymer compounds. In the melt spinning process, molten alloy is quenched by ejecting the material onto the surface of a rotating water-cooled wheel. However, the microstructure and magnetic properties of the NdFeB ribbons formed are very sensitive to the quenching process. A slow cooling rate produces ribbons that consist of larger grains and are characterized by low coercivities. This powder cannot be sintered to produce fully dense magnets without destroying the magnetic properties, but can be bonded with a resin to make permanent magnets. The crystals are randomly oriented (isotropic) and can be magnetized along any axis. The isotropic nature of the material limits the energy product to about 90 kJm3 . The resulting materials are commonly referred to as bonded type magnets. Hot pressed magnets may be able to push the boundaries of performance for bonded magnets, however, the properties do not compare to sintered NdFeB magnets.
While bonded NdFeB Magnets are significantly less powerful than sintered NdFeb magnets, there are some benefits from this process:
Sintered magnets are manufactured through a powder metallurgy processing and sintering route, which has provided us with the highest ever observed energy product for a permanent (hard) magnetic material, in excess of 400 kJm3. Sintered NdFeB based magnets achieve their superior intrinsic properties by virtue of a grain boundary phase that smoothes the boundaries during the liquid phase sintering process of magnet production.
The processing route for sintered NdFeB based magnets starts with an alloy that must first be broken into a powder. This is achieved most conveniently by exposing the material to hydrogen. The hydrogen enters the material in the spaces between the atoms and causes the material to expand breaking down into a coarse powder. This powder is further broken up by a jet milling stage which reduces the particle size to below 10 microns. When the powder has been broken down to a fine particle size, each particle of powder is a single crystal, which can be aligned in a magnetic field. This alignment is held in place by pressing the powder into a green compact, which is about 60% dense. The compact is then heated in vacuum and further densified, with the assistance of a liquid formed by the melting of the grain boundary phase. After sintering the magnets are quenched and then heat treated in order to achieve the optimum magnetic properties.
The magnet must then be machined to the final dimensions required for the intended application. Due to the large degree of shrinkage that occurs during sintering, which is greater in the direction of alignment, it is not possible to press compacts that will shrink to the exact size required.
Sintered NdFeB Magnets
While the sintered NdFeB process is much more tedious, the end product is also a powerful and efficient magnet that can perform at extremely high temperatures. Noveon Magnetics is the only domestic manufacturer of sintered NdFeB magnets, and we understand the importance of rare earth magnets in building an electric infrastructure. That’s why we sustainably manufacture sintered rare earth NdFeB magnets on U.S. soil, strengthening domestic supply chains and helping reduce our reliance on foreign suppliers and manufacturers.
The Sintered Advantage