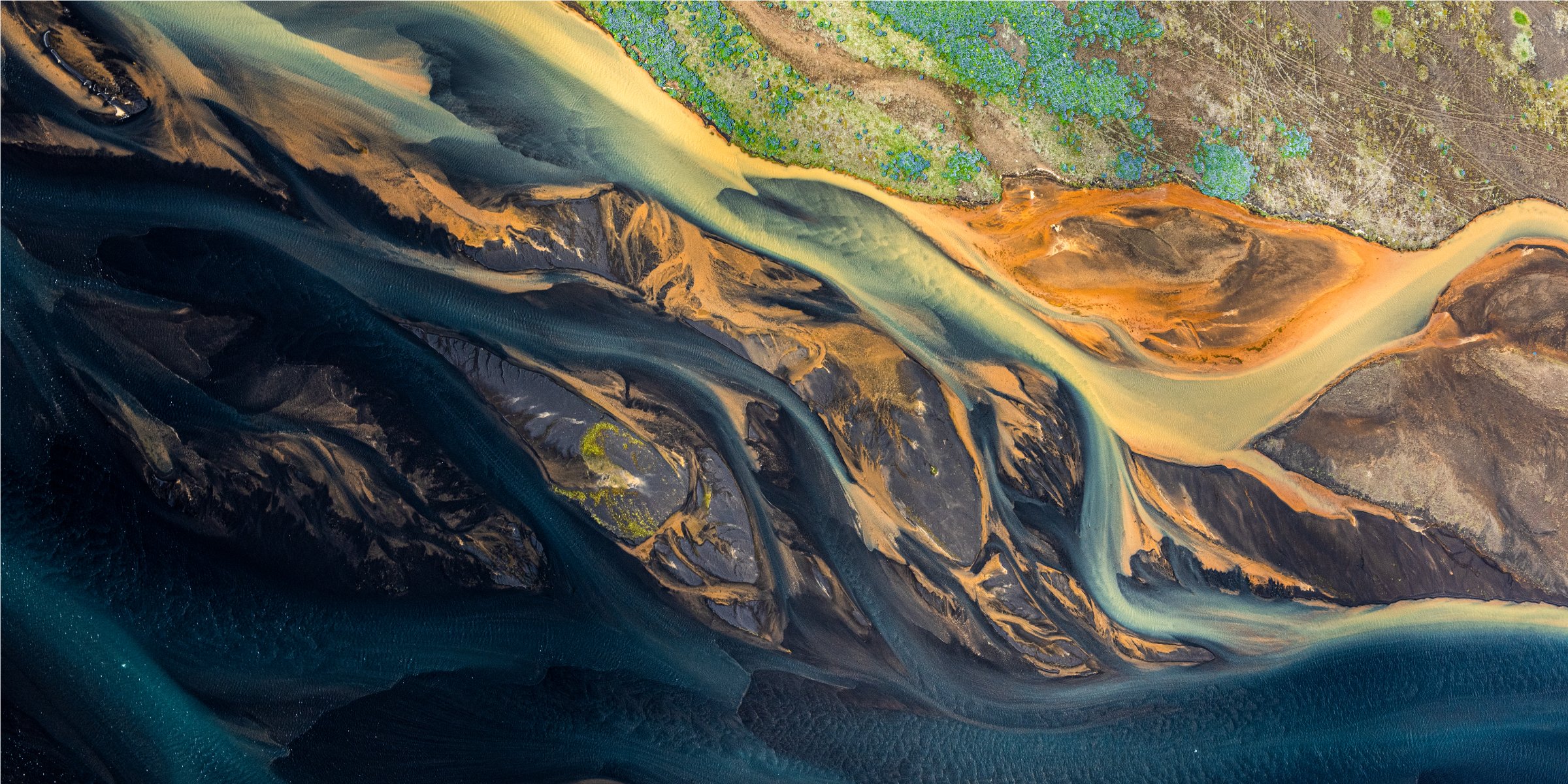
Meet The Texas Startup That Recycles Rare-Earth Magnets, Bypassing China
May, 2023
As demand rises and reliance on China becomes an issue of economic security, Noveon offers a solution.
At a factory in San Marcos, Texas, workers gather Bird scooters, computer hard drives, MRI machines and motors from hybrid cars in order to separate out the old rare-earth magnets so they can be ground down and shaped into new ones. These strong permanent magnets are everywhere, even if most people know nothing about them. They go into everything from electric vehicles to wind turbines to consumer electronics to missile guidance systems. Yet for years, the U.S. has been largely dependent on China for rare-earth processing. Noveon Magnetics, the startup behind this recycling effort, has a grand plan — and some patented technology — to make a dent in that dependance.
“We didn’t realize till the last decade how big the potential shortfalls were,” says Scott Dunn, Noveon’s cofounder and chief executive. “You don’t just get to turn on the spigot and produce these. They’re not a commodity.”
Magnets go into motors and generators that enable electricity to be transformed into motion and motion into electricity. Permanent magnets, made with rare earth materials, are a key element of the country’s efforts to decarbonize with electric vehicles and wind turbines. Because of their higher performance — allowing smaller, more powerful motors than alternatives — their use has spread and continues to rise. Global demand for rare-earth magnets will increase at 7.5% compounded annually through 2040, according to Adamas Intelligence.
Noveon, founded nearly a decade ago and currently expecting just $10 million in revenue this year, is a drop in the bucket for now. As with any precision manufacturing process, it has to run customers’ magnets through a battery of tests to qualify their use before scaling up. But with $150 million in equity funding — including a new $75 million investment led by energy investor NGP that has not been previously reported — at a valuation of approximately $300 million, it has set up its factory and is ready to crank up its output.
“We would need to build four or five factories to meet the demand of our customers.”
-Scott Dunn, Noveon cofounder and CEO
Dunn figures that once its San Marcos facility is at capacity, by 2024 or 2025, it will be able to churn out 2,000 tons of magnets under long-term supplier agreements, using a mix of recycled and mined rare-earth materials, and bringing in revenue of $250 million with 40% Ebitda at current magnet prices. After that, he hopes to set up similar magnet factories in Europe and Asia (outside of China), with a goal of reaching $1 billion in revenue within five years.
Scaling up an operation like this is extremely capital-intensive. Rare-earth prices have been volatile long term. And a key ingredient will be keeping the supply chains for the recycled materials running smoothly. But Dunn says that demand is so high that Noveon can’t even begin to meet its existing customers’ needs from its San Marcos factory. “We would have to build four or five factories to meet the demand of our customers,” he says.
Noveon isn’t the only company building a magnet factory in the U.S. to meet demand for domestically manufactured magnets as an alternative to China. MP Materials, a publicly traded $4 billion (market cap) firm that owns a major rare-earth mining and processing facility at Mountain Pass, California is currently building a magnet factory in Fort Worth, Texas with a capacity of 1,000 tons of finished magnets and a long-term agreement to supply General Motors. Two other U.S.-headquartered firms, Quadrant Magnetics and USA Rare Earth, as well as the German company Vacuumschmelze, have plans to establish U.S. magnet manufacturing facilities by 2026.
At the San Marcos factory: Noveon expects to churn out 2,000 tons of rare-earth magnets, bringing in $250 million in revenue, once it reaches capacity.
“If we can develop new processing, that is the key leverage point in getting our critical minerals supply re- or near-shored efficiently,” says Aidan Madigan-Curtis, a partner at the venture firm Eclipse, which has no relationship to Noveon.
For Noveon, it hasn’t been easy. Dunn and cofounders Peter Afiuny, Miha Zakotnik and Catalina Oana Tudor have spent years refining and patenting the technology and figuring out how to scale it up, helped by funding from the Department of Defense as well as money from private investors.
Typically, recycling permanent magnets results in decreased performance, but Dunn says that’s not the case with Noveon’s proprietary technology. Early customers include Nidec Motor, a large manufacturer of motors that’s part of Japan’s publicly traded ($30 billion market cap) Nidec Corp., and Eriez, a privately held manufacturer of industrial equipment — plus a number of customers that Dunn declines to name on the record.
Getting rare earth magnets, after all, is a big issue for the companies that need them, and with China reportedly considering prohibiting exports of certain rare-earth magnet technology following Washington’s restrictions on semiconductors, having homegrown supply is a big competitive advantage. “Permanent magnets are to motors what lithium is to batteries,” says Kirk Anderson, Nidec Motor’s director of government affairs. “These magnets, and critical minerals in general, are key to achieving the decarbonization goals the Administration is talking about.”
Blocks of recycled material that came from a motor: A step in the process of creating new magnets from old ones.
In 2021, the Commerce Department initiated an investigation into the effects on national security from imports of rare-earth magnets. The resulting report, released in February, concluded that the present quantities and circumstances of magnet imports “threaten to impair the national security,” and recommended bolstering U.S. magnet supply with a tax credit for domestic manufacturing and continued investment through the Defense Production Act, among other things. In April, Representatives Guy Reschenthaler (R-Pa.) and Eric Swalwell (D-Calif.) introduced a bipartisan bill to support domestic rare-earth magnet manufacturing with tax credits.
With critical minerals a major political issue, Texas Gov. Greg Abbott chose Noveon’s factory as the site of his State of the State address in February. Calling Noveon “a cutting-edge business in the critical field of rare earth elements,” Abbott said that we needed to decrease our reliance on China for rare earth minerals. “If that supply is ever disrupted, many of the things we do every day would come to a halt,” he said.
Dunn, 34, grew up in the town of Bel Air, Maryland, where his family had a privately held body armor and ballistics company. He studied at the U.S. Naval Academy, then transferred to the University of Southern California, where he studied environmental science.
The Dunns’ family business was small, but it got interesting work, like testing the bulletproof glass for presidential vehicles. Dunn first learned about recycling there, when his dad asked him as a teenager to figure out what to do with some leftover aluminum alloy known as 6061. “I’d been scrapping metal since I was 12,” he says.
After college, he continued on the recycling path, first at a Los Angeles firm that did energy retrofits and then, with cofounder Afiuny, a former colleague, on his own. Having learned just how much valuable metal could be recovered and recycled from old solar thermal water heating systems, their first effort focused on that niche. “We were selling direct to a copper smelter in the Philippines that was owned by a Japanese company,” Dunn says.
“These magnets, and critical minerals in general, are key to achieving the decarbonization goals the Administration is talking about.”
-Kirk Anderson, Nidec Motor’s director of government affairs
The business, at first called Urban Mining, morphed into Noveon after a professor of Dunn’s and a mentor of Afiuny’s nudged them to look at battery-related materials and rare earths. While the average consumer was oblivious to the importance of rare earth materials, the need for them to power electrification was becoming known in certain circles with the popularity of the hybrid Prius and the introduction of the first Tesla Roadster.
Following a 2010 incident in waters controlled by Japan but claimed by China, the Chinese government restricted exports of rare earths. Prices soared for two key rare earths used in magnets, with neodymium rising 750% and dysprosium rocketing 2,000%. “Peter and I were already a little bit on the trail,” Dunn says. “As a selfish capitalist, you could say, those are opportunity areas you want major exposure to.”
At first, Dunn and Afiuny, drawing on their recycling background, figured they’d simply try to consolidate rare-earth materials and sell it to separators in China and Japan. By 2012, the duo had traveled the globe — China, India, the Philippines, as well as the U.S. and Canada — looking at mines and separation facilities. “It was starting to become a bit of a buzz in defense circles in the U.S.,” Dunn says. “With hindsight, it seems like a no-brainer. But ten or 12 years ago, we had no idea what the issues could become like with China.”
In 2012, with the business at a standstill, Dunn and Afiuny attended a permanent magnet conference in Nagasaki, where they met Zakotnik, now the company’s chief technology officer, and Tudor. Zakotnik told them about his process for recycling rare-earth magnets. “This guy at the time had a big ponytail, so I thought, ‘This guy is a crazy scientist and I don’t believe him.’ We changed our trip and I went to China, and Miha kind of blew us away,” Dunn says.
Magnets for an electric motor or other industrial applications: Noveon's process allows it to produce high-end magnets from recycled materials.
Zakotnik, 47, who is from Slovenia and a chemist and materials scientist by training, had invented a process to recycle rare-earth permanent magnets through a powder metallurgy process. “As part of my Ph.D., I showed that our route could be used to recycle not once, but twice, three times, four times,” says Zakotnik, who published his research in 2008. Before joining forces with Dunn, he’d been a scientist at Yantai Shougang Magnetic Materials in China and a visiting professor at Beijing University of Technology researching rare-earth magnetic materials. But he’d always wanted to get his research into the real world.
“I tried to formulate this company five times. I failed five times,” he says. The problem, he says, was that starting a magnet recycling factory requires enormous amounts of capital upfront, without having a history as a business. “There is a lot of controversy in recycling magnets, that something like this is possible,” he says.
Returning to the U.S., Dunn and team started the business on the cheap in Delaware. Dunn’s father, who had sold the body armor and ballistics company to Intertek, was the first seed investor, putting in $1 million. They soon received their first government funds through the federal Small Business Innovation Research program, known as SBIR. In 2015, having received patents for their technology, they got an additional $25 million in equity and help with debt financing from the Kloiber family of Kentucky.
That gave them the funds to relocate to Texas, and to set up a pilot plant in Austin. The recycling process would not only give them an edge, they believed, but also allow them to make a historically hazardous process more energy efficient and environmentally friendly. Making magnets is typically a dirty process, one reason why processing them had migrated to China, and disposing of them is tough because they’re considered contaminants. Noveon’s process solved both of these problems. And once the company harvested the rare-earth materials from the old products, it recycled the remaining metal for scrap.
“Noveon makes the highest power or highest density magnets,” says Nidec’s Anderson. “They’re the best of the best.”
Terri Koebe, director of global strategic sourcing at Erie, Pennsylvania-based Eriez, first learned about Noveon from an engineer who’d attended a magnetics conference in Orlando, Florida in 2019. Soon the industrial firm had tested Noveon’s magnets, found them satisfactory and signed on as a customer. “They were very high quality and we were really impressed,” Koebe says. “It’s very complicated to extrapolate the rare earths from scrap material.”
Permanent magnets come in many varieties depending on their end use, and each one needs to be tested for months before it’s ready for mass production. It wasn’t long before word spread about Noveon’s American-made magnets.
“The demand for our product started to explode,” Dunn says. “We had automotive companies calling us saying, ‘How much can you make and when?’”
For a brief moment when tech stocks and SPAC deals were booming, Noveon was told it could be worth $1 billion. Today Dunn just laughs at that number. “I had to bust our banker’s chops a little bit,” he says. “I grew up in a family business. I’ve seen what happens when you pretend you have money on paper that’s not actually the value.”
After all, there are still big issues to figure out, including getting enough material with old rare-earth magnets to turn into new ones. Dunn says that while today most everything Noveon produces is made with recycled magnets, as the factory scales up to 2,000 tons its goal is to be at least 50% recycled material.
A bigger question long-term is whether viable alternatives to rare earths can be found. In March, Tesla announced that its next generation of electric vehicles would contain no rare-earth materials. While researchers at Adamas estimate that Tesla’s move would decrease global demand by just 2% to 3% in the near term, it has focused attention on the potential for alternatives that could lower costs and avoid supply-chain constraints.
For now, the supply-demand imbalance is so great that Noveon’s focus is scaling up its factory to give customers an alternative supply of American-made magnets. As Dunn says: “We don’t want China to just deliver us our quality of living and not have control of our destiny.”