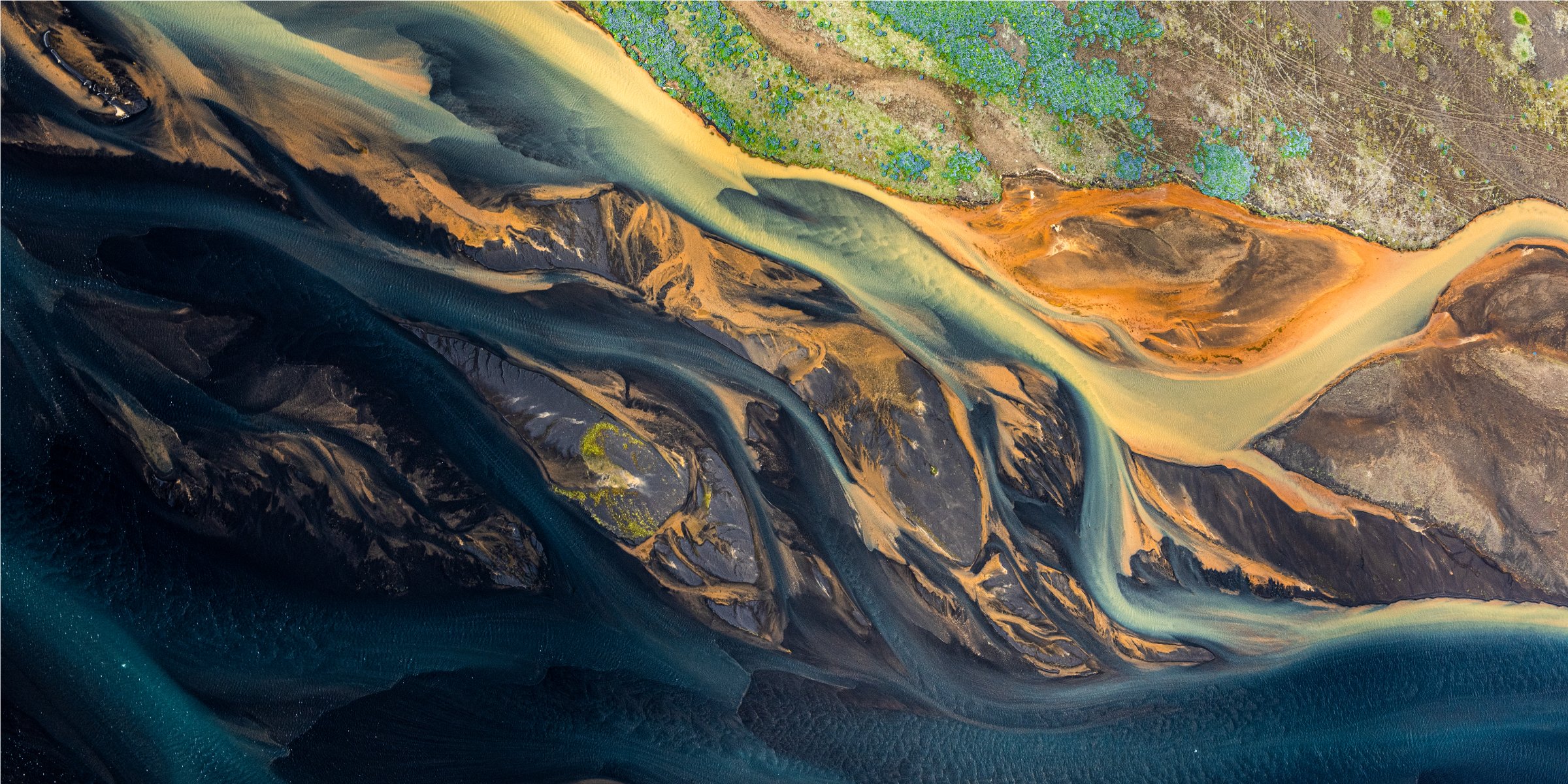
EcoFlux: Securing A Sustainable Electric Future
The emergence of affordable alternatives to fossil fuel-burning energy sources is one of the most important technological developments of the past century. But as we look to move away from fossil fuels in favor of lower-carbon technologies, a new problem has emerged: the shift to electrification is skyrocketing demand for environmentally harmful raw materials, including the kind of rare earth elements (REEs) used in magnet-powered applications.
Rare earth magnets are at the heart of electrification - Magnets are essential to nearly all high-tech, low-carbon technologies from the motors used to power electric vehicles, to renewable energy technology used in biogas and landfill facilities, to solar and wind farms and hydroelectric power stations. With the transition to electric power and renewable energy already underway, demand for REEs used to manufacture these critical magnets rising steeply. In fact, industry experts predict that global rare earth magnet demand will more than double by 2030 – to over 460,000 tons – and triple to over 675,000 tons by 2035.
Sustainability at Every Step
But we’re not only manufacturing superior magnets. At Noveon, we’re reimagining how magnets are manufactured by developing a process that reduces material waste and removes hazardous byproducts, resulting in far less adverse impact on our planet.
Noveon’s manufacturing process completely bypasses many of the steps that make traditional mining and manufacturing so hazardous to the environment. Our patented technology enables us to produce high-performance EcoFlux Magnets sustainably by:
Completely eliminating the most environmentally detrimental aspects of the value chain, including beneficiation, leaching, and solvent extraction
Avoiding hazardous, radioactive products associated with traditional production, such as thorium (Th) and uranium (U)
Drastically reducing demand for raw materials and associated environmental impact of mining activity
Achieving 90% energy savings as compared to traditional manufacturing – over 40% of which stems from the reduction in melting and alloying steps
Saving 11 tons of CO2 emissions for every ton of magnets we produce
Reducing overall environmental impacts by between 30% - 50%
Endless Waste Brings Endless Opportunity
With our breakthrough technology, we’re offering the world a new and superior magnet. And our manufacturing process leverages the potential for recycling end-of-life magnetic materials at scale to manufacture magnets even more powerful than those they replace.
Currently, less than 1% of the world’s rare earth elements are recovered or recycled, leaving behind an approximately 600,000-ton supply of end-of-life rare earth magnet material with enormous untapped recycling potential – until now. Noveon’s innovative Magnet-to-Magnet recycling technology is, for the first time, establishing a scalable market for recycling rare earth magnets.
Noveon’s high-performance EcoFlux magnets are powering a more sustainable, electric future. And by offering a recycling capability that maximizes recovery, promotes sustainability, and allows us to eliminate our dependence on traditional sources, we’re doing it without added costs to our planet.
EcoFlux: Power Without Compromise
With our high-performance EcoFlux magnets, we’re redefining the possibilities of electric energy, and we’re doing it sustainably. Our breakthrough technology allows us to design and engineer composition and microstructure to improve performance. EcoFlux magnets can meet requirements across the entire performance range, high-temperature applications in particular.
Our high-performance EcoFlux products are designed to exact specifications for a given application, perform at higher temperatures and in harsher environments than traditional rare earth magnets, and exhibit higher magnetic flux, higher coercivity, increased resistivity, and better stability while reducing the amount of heavy rare earth elements required by at least 20%.
Noveon’s technology is able to capture waste magnetic material to support our manufacturing process directly, using our existing infrastructure to deliver superior EcoFlux magnets from 100% recycled, sustainably sourced materials – magnets that can power a clean, electric, and energy-efficient economy.
August, 2022
The Paradox of Electrification
We cannot achieve our clean energy goals without magnets made from REEs, but meeting the demand needed to keep up with the growth of low-carbon technologies comes at its own environmental expense. The impact of mining involved in traditional production is incredibly energy-intensive, often degrading the environment while producing a high volume of material waste.
For every ton of rare earth elements produced, the mining process yields 13kg of dust, 9,6000-12,000 cubic meters of waste gas containing dust concentrate, hydrofluoric acid, and sulfur dioxide, 75 cubic meters of wastewater, and one ton of radioactive waste. Furthermore, once REEs are extracted, traditional magnet manufacturing includes environmentally harmful beneficiation, leaching, and solvent extraction processes that are both energy intensive and involve the release of radioactive byproducts such as thorium (Th) and uranium (U).
The environmental consequences that stem from REE mining and rare earth magnet manufacturing begs the question: how can we pave the way for an electric, low-carbon future without leaving a new set of environmental hazards in our wake?