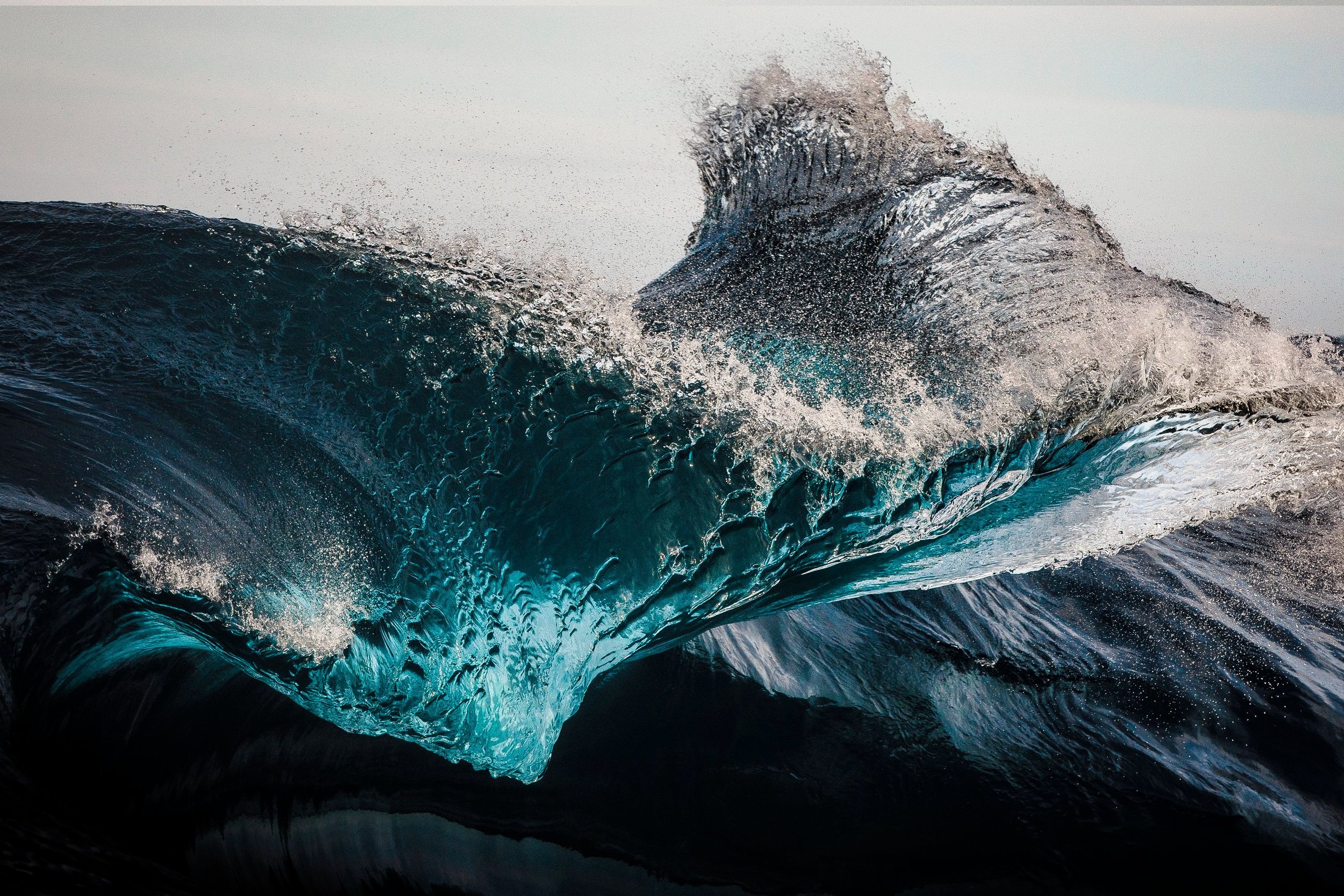
our process
A WHOLE NEW APPROACH | 01/09
Re-envisioning manufacturing.
At Noveon, we didn’t just set out to manufacture a better magnet. We set out to reimagine how we manufacture magnets by developing a process that cuts down on material waste, removes hazardous byproducts and sidesteps geopolitical uncertainty — a process industry so desperately needs and the market clearly demands.
How did we do it?
It all starts with the process: Our groundbreaking production process is comprised of state-of-the-art technology, automation and, most importantly, a team of visionaries committed to changing the future of high-tech manufacturing.
INDUSTRY-LEADING TECHNOLOGY | 02/09
Power without compromise.
With our breakthrough technology and revolutionary manufacturing process, we’re offering the world a new and superior magnet. We also offer a solution that takes advantage of recycling end-of-life magnetic materials — at scale — to manufacture magnets even more powerful than the ones they replace.
With our high-performance EcoFlux magnets, we’re redefining the possibilities of electric energy, and we’re doing it sustainably: using less energy, less rare earth materials and causing less harm to our planet. We produce magnets with higher magnetic flux, higher coercivity, increased resistivity and better thermal stability by optimizing the use of materials, virgin or recycled.
GBE® technology
GBE® technology represents the state of the art in magnet manufacturing. Whether used in conjunction with M2M® technology or stand-alone, this technology is used to create our high-performance EcoFlux magnets with superior properties and optimized composition.
M2M® technology
Our M2M® technology utilizes waste or recycled magnetic material as a feedstock to support our magnet manufacturing process. The resulting EcoFlux magnets maintain consistent composition and exhibit superior performance tailored to spec even with end-of-life feedstock used as a raw material in production.
CLOSED-LOOP SUPPLY CHAIN | 03/09
A resource breakthrough.
Currently, less than 1% of the world’s rare earth elements (REEs) are recovered or recycled. The potential sources of rare earth material for recycling are massive, mirroring demand/consumption itself. Our supply of recovered magnetic materials comes from end-of-life channels and diverse material streams, including motors, energy systems, medical devices, data storage, etc. With massive amounts of magnet supply sitting idle in our landfills, we offer the possibility to create recycling solutions that maximize recovery, promote sustainability and enable us to eliminate our dependency on traditional sources.
Since our production process can utilize end-of-life magnets, we’ve effectively created a closed-loop supply chain. That means we — and, by extension, our customers — are no longer subject to the pricing and availability risks that have challenged industry for years. And we no longer have to accept the burden that mining and manufacturing places on the environment.
CHART | N-005
Sustainable Recovery Circular Economy
1. Generation
End-of-life (EOL) equipment containing NdFeB magnets such as MRIs, electric motors, HDDs, HEVs, etc.
2. Collection
We design and build collection programs to collect material from operational, pre-consumer and post-consumer waste streams.
3. Separation
Rare earth permanent magnets are harvested from EOL products using a focused extraction methodology. No shredding technology is used.
4. Sorting
Materials are separated into individual components (magnets, steel, Al, Cu, plastics, etc.) using automated tools.
5. Recovery
100% of waste magnets are recycled as a feedstock into our production stream.
6. Design & Production
New products (magnets and assemblies) are created from recycled materials.
7. Export
Finished rare earth magnet products are shipped to customers worldwide.
8. Use
Magnets power motors in high-performance applications such as automotive, clean energy, medical, aerospace and defense, consumer, industrial automation, construction and oil and gas.
ENVIRONMENTAL IMPACT IN MANUFACTURING | 04/09
All the difference through a different approach.
The value chain involved in legacy mining and magnet production is incredibly energy-intensive and destroys the environment while producing a high volume of material waste. We take an entirely different approach.
EcoFlux magnet advantages:
100% recycled feedstock capable
>90% energy efficient vs. traditional manufacturing
11 tons reduction in CO2 emissions per ton of magnet produced
CHART | N-012
Noveon vs. Key Competitors
Note:
EcoFlux is more energy and resource efficient than traditional manufacturing.

We no longer have to accept the burden that mining and manufacturing place on the environment
STEPS REQUIRED FOR MANUFACTURE | 05/09
High-quality finished products in far fewer steps.
Our process enables us to eliminate fundamental — and environmentally hazardous — steps, including mining, separation and metal production.
SMART MANUFACTURING | 06/09
Smarter manufacturing. Smarter products.
Efficiency is a touchstone at Noveon, and it begins with our approach to manufacturing. To increase energy efficiency and help produce the most advanced magnets in the market, we implement a digitalization process we call “smart magnet manufacturing.” This allows us to continuously improve quality while adding value to our solutions.
AI enhanced with a human touch.
We employ neural networks and artificial intelligence that rely on a robust information database to constantly self-improve our process. Our smart technologies feature Automation; Quality Control; AI Inspection; Data Mining & Text Mining; AI (&ML/DL) Material Informatics Platforms; Analysis & Traceability; and Cybersecurity.
Quality assurance at every step.
We control every aspect of the magnet production process, from end-of-life materials used in manufacturing to alloys, mixing, blending, milling, pressing and heat treatment. All quality control occurs in real-time, accompanied by process monitoring and self-correcting actions. Our process control reduces overall manufacturing risk and ensures high-quality products with repeatability and with reduced failures. For our final inspection, we employ proprietary systems (hardware, vision and AI). And, for the first time ever, we’re offering a 100%-part inspection of defects and critical-to-quality characteristics (CTQs), including dimensional tolerances and coating thickness.
ASSEMBLY | 07/09
Beyond magnets: Custom-engineered assemblies.
In addition to producing magnetic materials and applications, we support the design and assembly of large-scale, advanced components and magnetic assemblies — which are scalable to any size and degree of complexity. All forms of processing steps — from the development of magnetic alloys to coating and magnetization all the way through assembly and final inspection — are conducted in our vertically integrated production facility right here in San Marcos, Texas. With our capabilities, we can manufacture one-off prototypes or fully automated, large-volume magnet assemblies.
And since all magnetic materials are manufactured in-house, our experts can easily adjust the manufacturing process to optimize the final performance of the completed assembly.
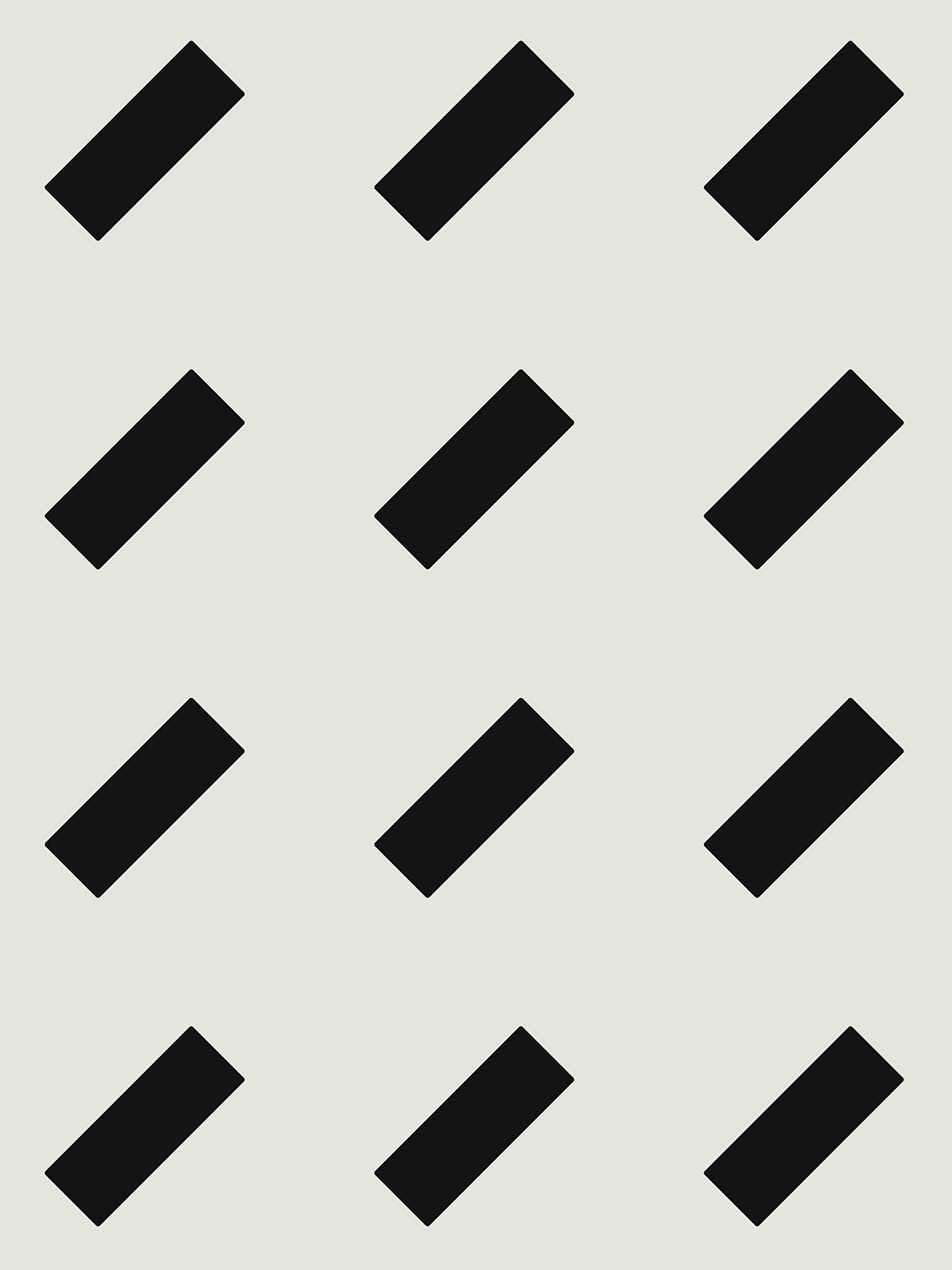
TECHNICAL AND ENGINEERING SUPPORT | 08/09
We’re with you the whole way.
We believe proper technical and engineering support for our customers’ application engineers is critical when developing custom-built solutions — especially during the early stages. That’s why we employ a full suite of support services for development, testing and evaluation throughout all stages to ensure we’re in lockstep with our customers’ vision and deliver the most cost-effective and highest-performing solution.
COMMITMENT | 09/09
Our goals are lofty. We intend to achieve them.
At Noveon, we deliver world-class solutions to our clients guided by our principles and commitment to build a more high-tech, sustainable future — and it is reflected in everything we do as an organization. Our focus on technology, improvement, automation, quality, environment and health and safety initiatives enables us to improve overall performance and bring in leadership with a shared passion for a clean energy ecosystem.